DECISION MAKING
You are required to answer the following three questions. The assignment must be completed individually and submitted before the due date to avoid any late penalties. Please make sure you follow the guidelines noted in your subject outline especially those relating to presentation of written work, late policy and academic integrity.
Assessment Description
CASE STUDY 1
Costello Corporation produces two grades of wine from grapes that it buys from California growers. It produces and sells roughly 600,000 gallon jugs per year of a low cost, high-volume product called Valley Fresh. Costello also produces and sells roughly 200,000 gallons per year of a low-volume, high-cost product called Costello Valley. Costello Valley is sold in 1-liter bottles. Based on recent data, the Valley Fresh product has not been as profit table as Costello Valley. Management is considering dropping the inexpensive Valley Fresh line so it can focus more attention on the Costello Valley product. The Costello Valley product already demands considerably more attention than the Valley Fresh line.
Frankie Costello, president and founder of Costello, is sceptical about this idea. He points out that for many decades the company produced only the Valley Fresh line, and that it was always quite profitable. It wasn’t until the company started producing the more complicated Costello Valley wine that the profitability of Valley Fresh declined. Prior to the introduction of Costello Valley, the company had simple equipment, simple growing and production procedures, and virtually no need for quality control. Because Costello Valley is bottled in 1-liter bottles, it requires considerably more time and effort, both to bottle and to label and box, than does Valley Fresh. The company must bottle and handle 4 times as many bottles of Costello Valley to sell the same quantity as Valley Fresh, since there are approximately 4 litres in a gallon. Valley Fresh requires 1 month of aging; Costello Valley requires 1 year. Valley Fresh requires cleaning and inspection of equipment every 2,500 gallons; Costello Valley requires such maintenance every 250 gallons. Frankie has asked the accounting department to prepare an analysis of the cost per gallon using the traditional costing approach and using activity-based costing. The following information was collected.
Valley Fresh
page2image18312
Costello Valley
Direct materials per gallon
page2image21080 page2image21400
$1.35
page2image22328 page2image22648
$3.60
Direct labour cost per gallon
$0.75
Save your time - order a paper!
Get your paper written from scratch within the tight deadline. Our service is a reliable solution to all your troubles. Place an order on any task and we will take care of it. You won’t have to worry about the quality and deadlines
Order Paper Now$1.50
Direct labour hours per gallon
0.05
page2image30496
0.10
page2image31424
Total direct labour hours
30,000
20,000
page2image35336
Activity Cost Pool
page2image38160
Cost Driver
page2image39232 page2image40056
Estimated overheads
page2image41288
Expected use of cost drivers
page2image42912 page2image43232
Expected use of cost drivers per product
page2image44904
Valley Fresh
page2image46448
Costello Valley
Grape processing
Cart of grapes
$146,000
8,000
6,000
page2image53320
2,000
Aging
Total months
$420,000
3,000,000
600,000
page2image60080
2,400,000
Bottling and corking
page2image62712
Number of bottles
page2image64296
$210,000
1,400,000
page2image66088
600,000
page2image67488
800,000
Labelling and boxing
page2image69800
Number of bottles
page2image71384
$140,000
1,400,000
page2image73176
600,000
page2image74576
800,000
Maintain and inspect equipment
Number of inspections
page2image78656 page2image79152
$234000
page2image80720
1,040
240
page2image82856
800
page2image84920
Required:
Write a memo to Frankie Costello providing a brief description of what is activity based costing as well as an explanation of how the traditional approach can result in distortions.
Hint: You should support your discussion by calculating and comparing the total manufacturing cost per gallon for both products under both traditional costing systems as well activity based costing.
Looking for a similar assignment? Our writers will offer you original work free from plagiarism. We follow the assignment instructions to the letter and always deliver on time. Be assured of a quality paper that will raise your grade. Order now and Get a 15% Discount! Use Coupon Code "Newclient"
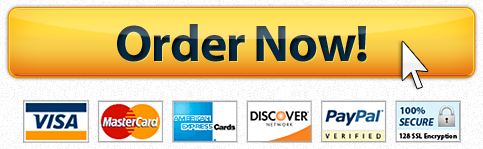